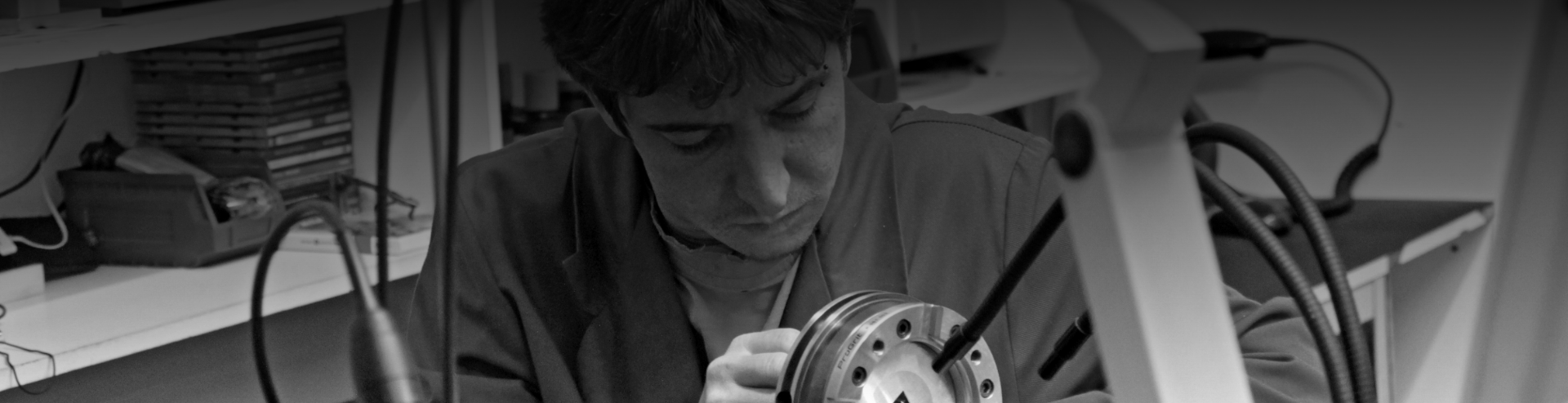
Multi Impression Tooling
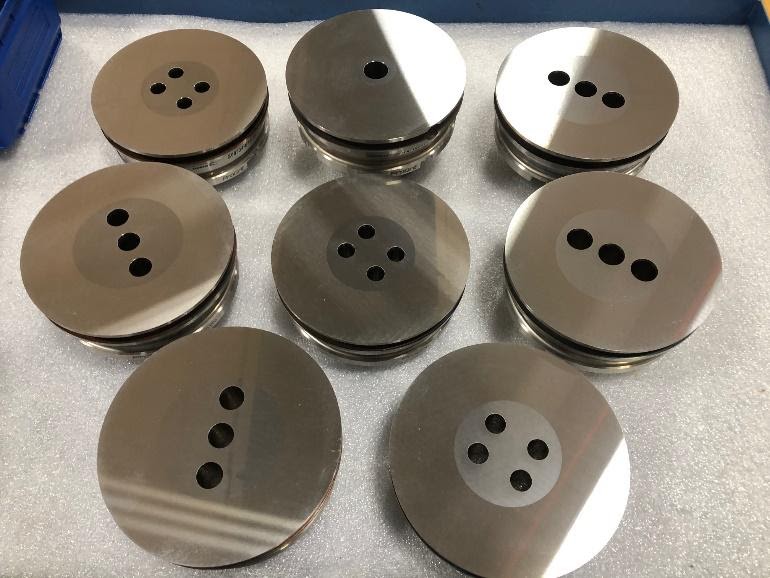
Multi Impression Tooling – with SMED built in
No matter what activity our clients are involved in we work on projects where output and uptime of the process is key. We look to optimise the number of parts produced within each cycle even on complex production runs. Add this to extensive material knowledge, our clients have access to true world class efficiency levels.
An example of this is a client working in ceramics, the press was stopped every 24 hours to change key parts due to wear. With careful optimisation the process runs for 4 weeks without a stoppage for wear.
The knowledge within the n group allows us to give consultancy for companies wishing to improve their productivity through SMED strategies.